The hydraulic breaker hammer of an excavator can be said to be a commonly used accessory for excavators. It is mainly used in many jobs such as road construction, building demolition, and rock crushing in cities. Although the reward for using hydraulic crushing is higher. But the damage to the excavator is also very large.
The vibration frequency and impact force of different hydraulic breakers cause different damage to the excavator arm and bucket rod, so it is necessary to choose an excellent hydraulic breaker manufacturer. The core Tiedou excavator hydraulic pump has the highest pressure when using hydraulic crushing. In particular, high-frequency and long-term use increases the load of the hydraulic pump, accelerates wear, and long-term work will also cause the hydraulic oil temperature to rise. Many damages require regular maintenance. At present, some manufacturers have provided buffer devices for hydraulic breakers, but they can only reduce the damage to the excavator arm and bucket rod, but cannot reduce the working pressure of the hydraulic pump.
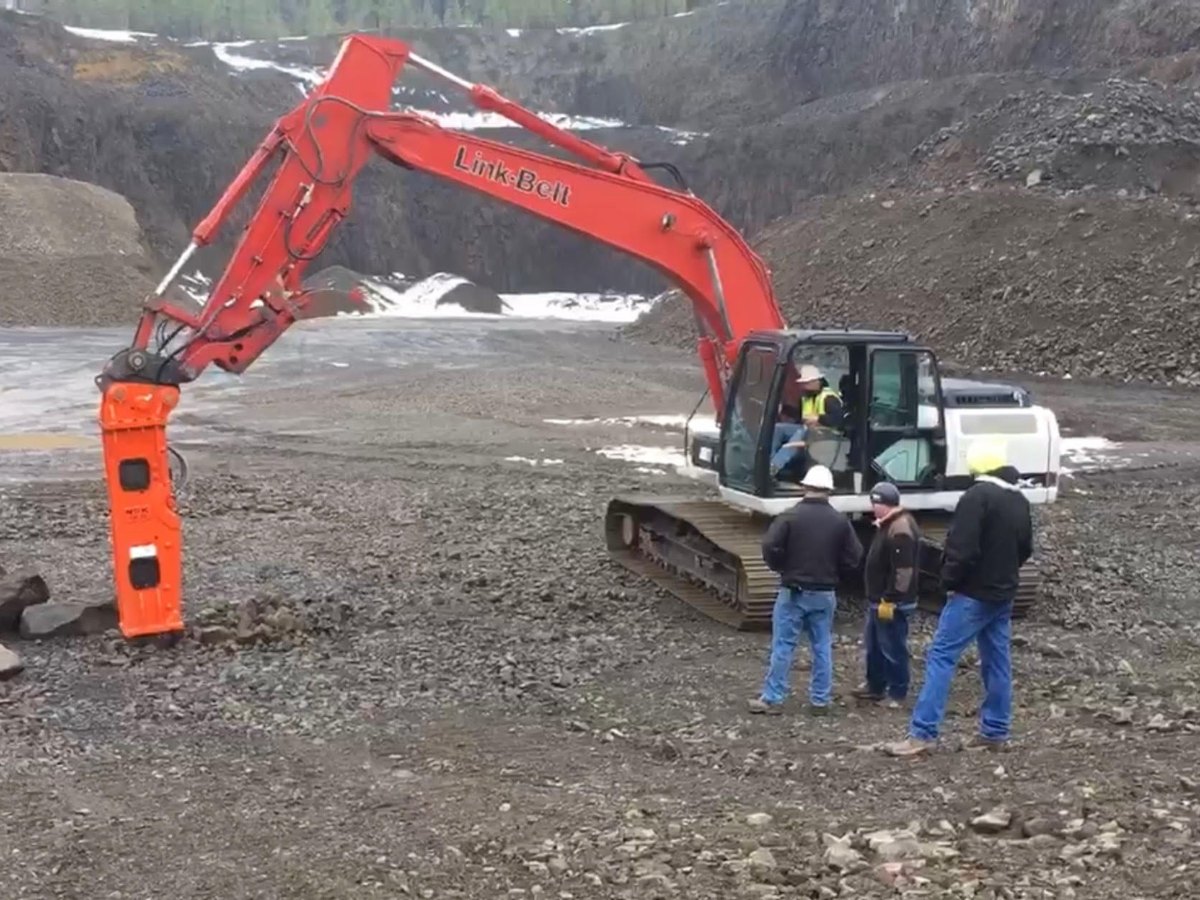
1. Main impacts
a. Increased structural stress
Arm and bucket rod: The breaker generates strong impact force when working, which is transmitted to the arm and bucket rod, causing these parts to bear greater stress than ordinary excavation work. Long-term use of the breaker may cause accelerated wear of the joints and connecting pins of the arm and bucket rod, and may even cause deformation or breakage.
Hydraulic system: The breaker requires a high flow of hydraulic oil, and long-term operation will cause the temperature of the hydraulic system to rise. If the temperature of the hydraulic oil is too high, it will reduce the lubricity of the hydraulic oil and accelerate the wear of the hydraulic pump and valves. The breaker will generate hydraulic shock when starting and stopping, which will damage the hydraulic pump, valves and pipelines.
b. Vibration and shock
Vibration transmission: The violent vibration of the breaker when working will be transmitted to various parts of the excavator. Long-term vibration may cause loose connection parts, loose bolts, and even cracking. Vibration will also accelerate the wear of various connecting parts, bearings and pivots, shortening their service life.
Structural fatigue: Frequent use of the breaker will cause the stress concentration parts in the excavator structure to bear higher loads, increase the risk of metal fatigue, and eventually may cause cracks or breaks.
2. Preventive measures
a. Choose the right breaker
Matching model: Make sure the specifications and weight of the breaker match the model of the excavator. Overweight or oversized breaker will put too much burden on the excavator and increase the risk of failure.
Quality assurance: Choose reliable brands and manufacturers to ensure the quality and performance of the breaker. High-quality breaker is not only efficient, but also reduces damage to the excavator.
b. Correct installation and operation
Professional installation: Ask professional technicians to install the breaker to ensure that it is firmly and safely connected to the excavator to avoid failures caused by improper installation.
Correct operation: Avoid excessive use during operation, and the continuous working time should not be too long to avoid the breaker and excavator from being subjected to high loads for a long time. When using a breaker, try to keep the hammer head vertical and avoid hitting it at an angle, which can reduce stress concentration and equipment wear.
c. Regular inspection and maintenance
Daily inspection: Check the breaker and its connection parts before and after work every day to ensure that there is no looseness, cracks or oil leakage. Check the hydraulic oil level and quality, and add or replace the hydraulic oil in time.
Regular maintenance: Replace the hydraulic oil and filter element regularly to keep the hydraulic system clean and at normal working pressure. Check the hydraulic pipeline, joints and seals to ensure that there is no oil leakage or damage.
d. Use buffer device
Shock absorber: Install shock absorber pads or other buffer devices to reduce the vibration and impact generated by the breaker when working, and protect the structure and hydraulic system of the excavator.
3. Pay attention to operating skills
Avoid empty hitting: The hammer hitting in the air is not only inefficient, but also causes unnecessary impact on the connection between the breaker and the excavator, increasing the risk of wear and damage.
Proper rest: Give the equipment proper rest time during long-term work to prevent overheating and excessive fatigue of the hydraulic system. Intermittent working method can be used to extend the service life of the equipment.
Correct positioning: When using a breaker, ensure that it is accurately positioned to avoid skewed strikes and uneven force to reduce stress concentration and equipment wear.
No matter how you use hydraulic crushing, damage to the excavator is inevitable, but the maintenance cycle of the excavator can be further shortened to reduce wear and tear and increase life. Friendly reminder: After the hydraulic crusher is installed, it is necessary to take appropriate time to reduce the abnormal wear caused by the high temperature of the hydraulic pump.