The boom and dipper of the excavator are the most commonly used connecting parts in the entire excavator equipment. If the excavator is abnormal, the operation of the boom and dipper can clearly feel whether there is a problem with the hydraulic system and performance of the excavator equipment. The wear, breakage, abnormal noise, and shaking caused by the gap of the boom and dipper are common problems. This issue will teach you how to check and troubleshoot.
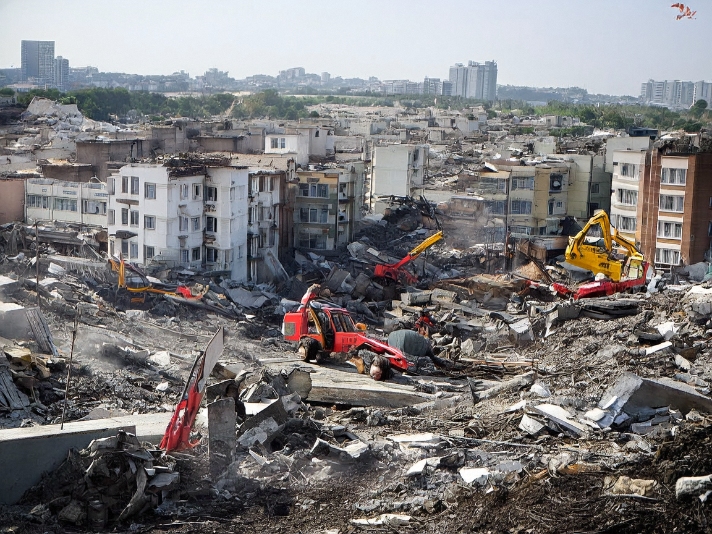
1. Common faults and troubleshooting of the boom
As the connecting part between the excavator body and the dipper, the boom bears a large pressure. If the boom is found to be slowly lifted, it is necessary to check the hydraulic system and hydraulic pipeline. If there is an abnormal sound in the boom, it is necessary to check whether the boom pin and sleeve are worn as soon as possible. In addition to daily maintenance and adding grease, it is also necessary to check whether there are foreign objects in the hydraulic cylinder and whether the supporting components are worn. If the boom cannot maintain the working height, it may be due to internal leakage in the hydraulic cylinder, damage to the piston and seal, and check whether the one-way valve of the control valve is faulty, resulting in the inability to maintain oil pressure. The presence of debris and particles in the hydraulic oil may also cause the valve to be not closed tightly, resulting in pressure relief. Fracture and crack, long-term load work and improper operation can easily lead to cracks or even fractures in the upper layer of the boom. In addition to reducing the load work, it can be effectively avoided by reinforcing both sides of the boom and welding with high-strength steel plates later.
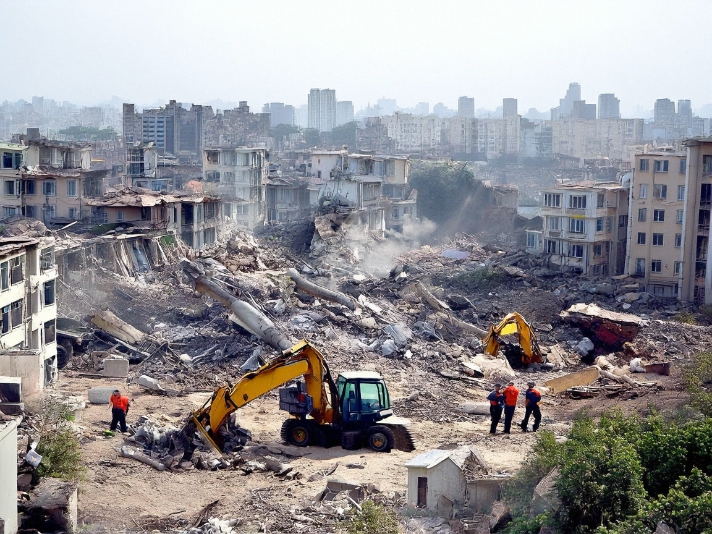
2. Common faults and troubleshooting methods of the bucket arm
The bucket arm is weak and slow to move. First check whether there are problems with the hydraulic system and the cylinder pressure relief link supporting components, and check whether the pipeline is blocked and leaking. The bucket arm makes abnormal noises and shakes. Check the wear of the bucket arm pin sleeve and bushing and foreign matter. Daily shortening and adding grease according to different work types can increase and reduce wear. The bucket arm cannot be fixed in position. Check whether the hydraulic cylinder leaks internally and the seal leaks. The one-way valve failure in the hydraulic system or the quality of the hydraulic oil causes the failure. The bucket arm, as a working material in contact with the bucket, produces bumps and wear. The wear can also be reduced by reinforcing the inside of the bucket arm.
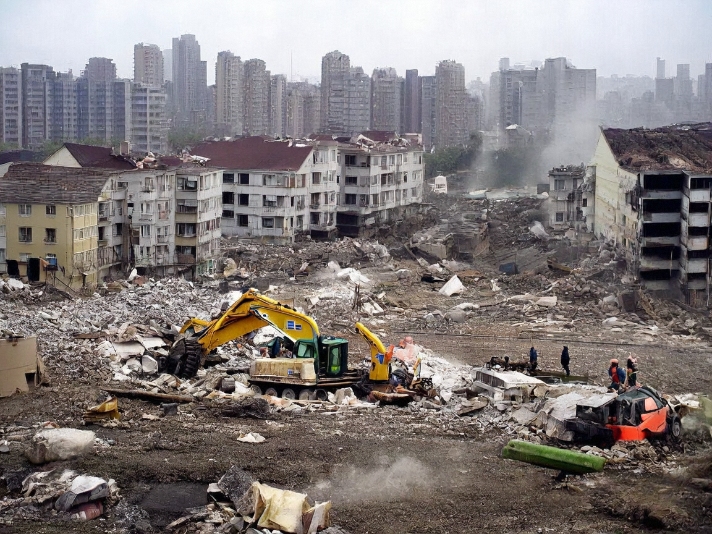
3. Prevention and maintenance
The boom and the dipper have simple structures, and wear mostly occurs on the bushings and pins. In addition to adding grease, wear can be reduced by cleaning foreign objects in key positions during daily use to avoid long-term load working conditions. If it cannot be avoided, regular inspections are required in addition to the reinforcements introduced. Once the equipment is abnormal and is not paid attention to, accelerated wear will cause deformation of the boom and dipper under working pressure, and only a higher cost can be spent on replacement later.